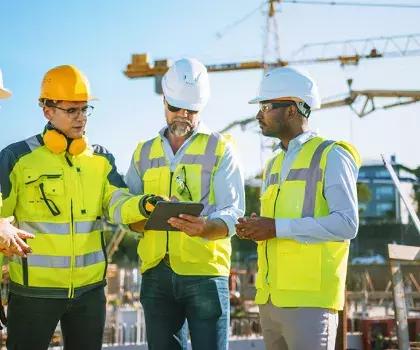
How Construction Sites Have Become Safer
The construction industry was once one of the most dangerous industries to work in. Now, it is one of the most regulated. Read more to discover how it evolved and how we can help you implement the current Health and Safety regulations.
A Potted History
This 19th century was a dangerous time to be a manual labourer. If you were building railways then you were particularly at risk, with three workers losing their lives for every mile of track that was laid in the UK.
The digging and construction of the Woodhead Tunnel, for example, between Manchester and Sheffield, took six years to build and killed 32 workers and seriously injured 140. Nearly thirty more people died from cholera due to the unsanitary living conditions.
Progress on health and safety in construction was very slow. It wasn’t until 1974 that the Health and Safety at Work Act was passed, but that year still saw 166 construction workers die, which was a quarter of all work-related deaths.
This act placed more emphasis on employer and employee responsibility and introduced a system that was more goal-based and less prescriptive than any that had gone before. It also consulted and engaged employers and employees in the process. The Health and Safety Executive was formed shortly after as well, to help enforce the law.
The 1990s saw innovation help construction sites become safer, especially for those working at height. High reach excavators and cherry pickers enabled workers to work in a safer way. PPE became more significant as the Personal Protective Equipment at Work Regulations came into force in 1993.
In 2000, the ten-year campaign “Revitalising Health and Safety Strategy” was launched. It was launched at a time when the proportion of people injured at work was the same as in the early 1990s, and the campaign aimed to improve the safety of the workplace. There was a push towards better training, more worker engagement, behavioural change, and a closer-knit way of working together.
Welfare Regulations
Above we discussed the deaths due to living conditions way back in the 19 th century. Today, the HSE provides guidelines on the minimum welfare facilities that you, as a contractor or co-ordinator, must provide for your workers.
They need toilet and washing facilities, a place to prepare and eat food, and somewhere to store their clothing, ultimately and area where the workers can enjoy their time break from the working environment. Good welfare facilities can benefit wellbeing, and ensure your workers are productive, comfortable and happy.
Toilets – if possible, flushing toilets and running water should be provided. If this is not practical, supply facilities with a built-in water supply and drainage tanks. They should be ventilated, lit and regularly cleaned and maintained.
You should also consider how many toilets you need, as well as whether you need to provide separate men’s and women’s facilities. This is something that Elliott can advise you on, to ensure that you are providing the right number of toilets for the number of workers.
Washing facilities – these should include:
a supply of clean hot and cold, or warm, water (which should be running water so far as is reasonably practicable)
soap or other suitable means of cleaning
towels or other suitable means of drying
sufficient ventilation and lighting
sinks large enough to wash face, hands and forearms.
If the work is particularly dirty, or your workers are exposed to hazardous materials, you will need to provide showers separately from the main facilities – and if they are working with lead, asbestos or compressed air, your workers will need specialist facilities.
Drinking water – where possible, drinking water should be supplied directly from the mains, with cups provided at the outlet.
Changing rooms and lockers – construction sites should be able to securely store personal clothing not worn on site and protective clothing needed for site work. Changing facilities for men and women should be separate.
Rest facilities – designed for your workers to be able to take a break out of the elements and eat meals, rest facilities should have seating with backs, tables and a means for heating up food and water for drinks. These facilities should be heated and provide a suitable environment for all workers. Most construction companies have learned the benefits of providing welfare which caters for all worker’s needs, assessing these needs at the earliest possible stage benefits the project and reduces unnecessary complications at a later date.
At Elliott, we can provide the welfare facilities that your construction site requires. All our facilities are designed to meet and exceed the regulations, giving your workers the support what they need to be productive and happy. We can also advise you on the numbers of facilities you might need for the duration of the project, the size of the site and the number of people you have on site. Elliott teams are well versed in all project variations and understand the benefits of working with the management company to ensures both a compliance and worker satisfaction.
Fire Regulations
Constructions sites are particularly vulnerable to fire, and if they do happen, they can affect a site in a number of ways, from delays and rebuild costs to injury and even loss of life. In the eighties, insurers were beginning to question whether insuring sites against fire was even commercially viable. That’s where the Joint Fire Code came in in 1992.
The code covers everything from design stages to construction, and generally applies to contracts with a value of more than £2.5million. Since its introduction, fire incidents on site have reduced significantly.
Here at Elliott, we understand the regulations and are able to help you ensure that your construction site is fire safe from the very beginning. Whether it’s help in setting up your site, or providing you with buildings that meet the regulations, we can give you the protection you need.
Our Fireflex modular buildings are specifically designed to give you enhanced fire protection, but with no compromise on the building layout that you want. For instance, you could have open plan offices, meeting rooms and even three-story buildings. They provide a minimum performance of 60 minutes (vs the 30 minutes of protection you get from a regular fire-rated building) and provide protection to the occupants and any adjacent buildings.
Setting Up A Site
We also provide our turnkey product, 360 services. This means that we can set your construction site up for you, to meet and exceed all the HSE regulations, and you and your workers can walk in and start work on your project straight away.
Buildings are built in a controlled environment in our depots, and then brought to site to be fully
assembled, taking the majority of the risk away from the construction site.
Everything from climate control to generator hire to safety barriers, we can ensure that we are your one point of contact for setting up site, so you don’t have to consider the health and safety regulations in much detail. Instead you can rest assured that your site is compliant and ready to go.
If you’d like to discuss any of the points in more detail, please don’t hesitate to get in touch.